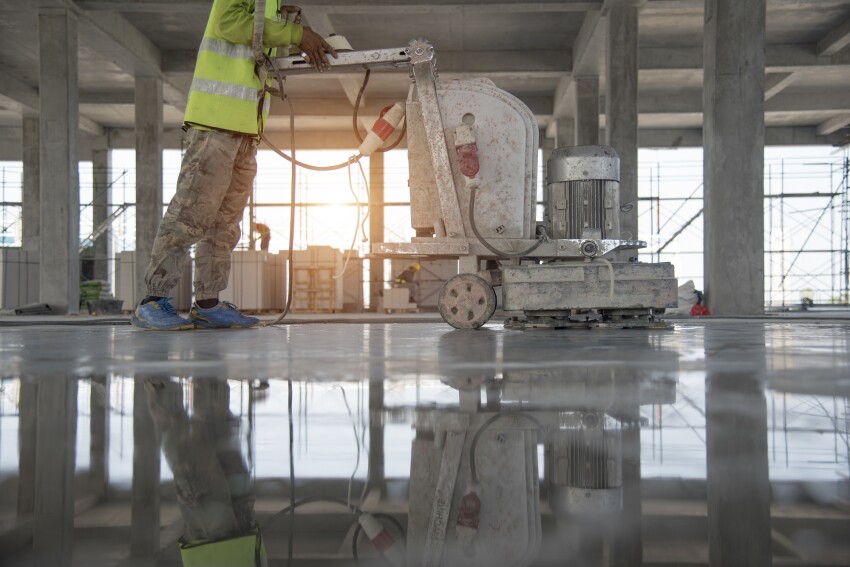
For years, the only approach to protecting concrete floors was to cover them with a film or membrane. Such products include acrylics, urethanes, epoxies and waxes. By their very nature, however, coatings are only a temporary solution. They are subject to delamination, scratching, chipping and wear. Eventually, they have to be replaced. This involves the expense of downtime, materials and labor. Some inexpensive coatings last only as little as 6 months to a year, so the associated maintenance costs are frequent and high.
Concrete Densification & Polishing takes a different approach to concrete floor protection. Rather than coating the surface with organic solids, lithium or sodium based silicate densifiers grows new crystals in the concrete. This reaction fills in the natural pores and voids in the concrete and provides a dense, hard surface that is easy to clean. The concrete is densified internally and inorganically. There is nothing to wear off the surface, nor is there anything to replace. The same reaction also makes the surface much harder and resistant to abrasion. In addition, the floor surface is rendered free of dust.
The polishing process that can take in up to 7 different stages of diamond polishing interspersed with a densifier application and a sealer application. The result is a highly polished, dense, abrasion resistant, light reflective floor finish.
Polished concrete can be treated with varying grades of diamond to provide a finish from ‘salt and pepper appearance’ up to a highly polished ‘super or premium’ type finish or anything in between.
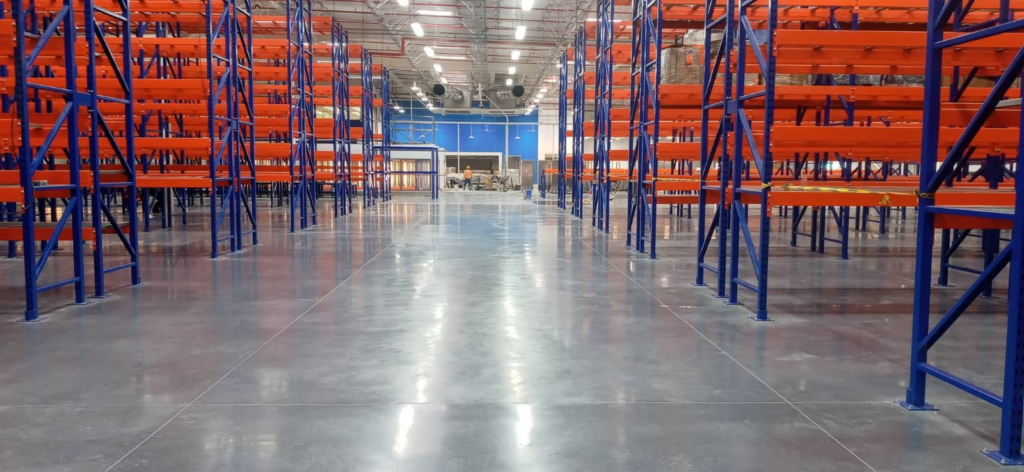
Advantages:
- Chemical-Resistant
- High Durability
- Environmentally Friendly
- Long Life-Span
- No VOC
- Low-Maintenance
- High Light Reflectivity
- Chemical & Solvent Resistant
- Cost effective